铝压铸模具公司
模具的保养是确保模具长期稳定运行、提高生产效率以及降低生产成本的关键环节。以下是一些关于如何保养模具的建议:定期清洁模具:模具在使用过程中会积累各种灰尘、油污和金属屑等杂质。这些杂质不仅影响模具的外观,还可能对模具的精度和性能造成影响,甚至导致产品质量下降。因此,定期清洁模具表面是非常必要的。在清洁时,可以使用软毛刷和特用的清洁剂轻轻刷洗模具表面,注意避免使用过硬的刷子或工具,以免划伤模具。及时修复模具损伤:模具在使用过程中难免会出现磨损、裂纹等损伤。压铸模具的设计需要兼顾产品的功能性和经济性,以达到较佳的性价比。铝压铸模具公司
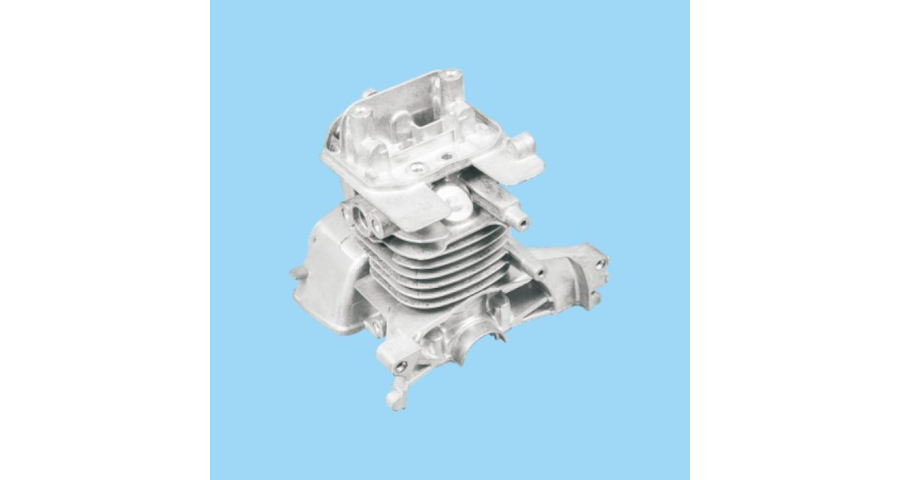
在使用压铸模具时,需要注意以下几点:首先,要严格按照操作规程进行操作,避免操作不当导致模具损坏;其次,要定期检查模具的磨损情况,及时更换磨损严重的部件;要合理控制压铸参数,如压力、温度、时间等,确保产品质量和生产效率。维护保养为了延长压铸模具的使用寿命,需要进行定期的维护保养。维护保养包括清洗模具、检查模具各部件的紧固情况、润滑模具运动部件等。此外,还需要对模具进行定期的维修和修复工作,如更换磨损严重的部件、修复模具表面的缺陷等。广东销售压铸模具哪家好采用氮气弹簧等先进部件,可以提升模具的开合效率和安全性。
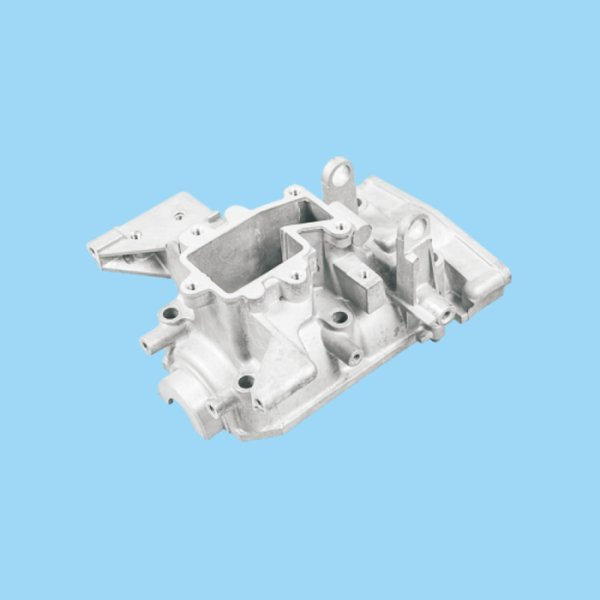
浇注系统设计1.内浇口位置和尺寸:内浇口的位置应根据铸件的壁厚分布、形状特点等确定,使金属液能够均匀、平稳地填充型腔,避免出现紊流和卷气现象。内浇口的尺寸则要根据铸件的重量、壁厚和压射速度等参数进行计算和优化。2.横浇道和直浇道设计:横浇道应具有足够的截面积和长度,以保证金属液在其中流动时保持稳定的速度和压力。直浇道的直径和长度要与压射系统相匹配,确保金属液能够顺利进入横浇道和型腔。冷却系统设计1.冷却水道布局:冷却水道应尽可能靠近型腔表面,且分布均匀,以实现对铸件的均匀冷却。水道之间的间距要合理,避免因冷却不均匀导致铸件产生内部应力和变形。2.冷却水道直径和流量:根据模具的大小、铸件的材质和壁厚等因素确定冷却水道的直径和冷却液的流量。一般来说,较大的模具和较厚的铸件需要较大直径的冷却水道和更高的流量来保证冷却效果。
模具在使用过程中也可能出现一系列问题,这些问题往往与模具的维护、保养和使用环境有关。例如:磨损和腐蚀:模具在使用过程中会受到金属液的冲刷、摩擦和腐蚀作用,长期使用可能导致模具表面磨损严重,甚至出现腐蚀坑、裂纹等缺陷。这些缺陷不仅影响铸件的成型质量,还可能缩短模具的使用寿命。变形和开裂:模具在使用过程中受到高温、高压等复杂应力的作用,如果模具材料选择不当或结构设计不合理,可能导致模具出现变形、开裂等问题。这些问题可能导致模具报废,给生产带来严重损失。操作不当:模具的操作和使用需要严格遵守操作规程和注意事项。如果操作人员技能不足或疏忽大意,可能导致模具在使用过程中受到损坏或出现故障。例如,错误的脱模方式可能导致模具损坏;不规范的清洁和维护可能导致模具表面受损或生锈。在模具制作前,需要进行详细的模拟分析,以预测可能出现的问题并优化浇注系统设计。
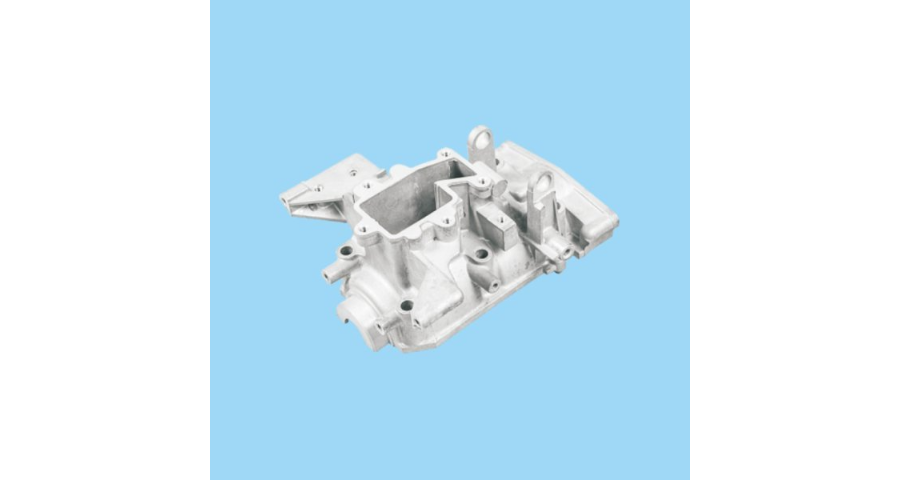
生产一个高质量的铝合金压铸件离不开精密且可靠的压铸模具。1.设计原则与要求设计一个质优的铝合金压铸模具首先要考虑的是模具的使用寿命、铸件的精确度和生产效率。模具设计需要利用先进的CAD/CAM系统进行三维建模,并结合铝合金的物理特性来优化型腔的结构、分流道的布局及冷却系统的设计。此外考虑到铝合金的腐蚀性,模具材料需选择耐腐蚀性强的合金钢,并进行适当的表面处理。2.材料选择与热处理模具钢的选择对压铸模具的质量起着决定性作用。常用的钢材有P20、718、H13等,它们具有良好的抛光性能、高耐磨性和抗热疲劳性能。在热处理过程中,通过淬火和回火等工序提高模具的硬度和韧性,以承受高压注入和快速冷却带来的热冲击。在汽车、电子、家电等行业中,压铸模具被广泛应用于生产各种复杂形状的零部件。宁波机械压铸模具制造
压铸模具的热处理工艺对其性能有着决定性的影响。铝压铸模具公司
产品分析主要是了解产品的结构、尺寸、材料性能等要求;模具结构设计则根据产品要求设计出合理的模具结构,包括分型面、浇口系统、冷却系统等;模具材料选择则需要根据产品材料、生产批量等因素选择合适的模具材料。制造阶段制造阶段包括模具加工、热处理、装配调试等。模具加工需要采用高精度的加工设备和工艺,确保模具的精度和表面质量;热处理则是通过加热和冷却的方式改变模具材料的性能,提高其硬度和耐磨性;装配调试则是将模具各部件组装在一起,进行调试和优化,确保模具能够正常工作。铝压铸模具公司
上一篇: 河南机械压铸模具供应
下一篇: 福建汽车压铸模具技术指导